The last couple of days were dedicated to printer projects and getting them together. I had a short list of things to pick up and a short list of things to get done aside from those parts.
- build a direct drive mount
- build a filament dry box
- build a filament roller
- build a printer enclosure
It's cool because I'd already bought all the materials for these projects in the form of filament and leftover house material. The enclosure and dry box are just simple plywood boxes really. Some folks just use Rubbermaid boxes, but in my case that would require spending money that I don't have. I'm currently saving up whatever crypto I can get my hands on to buy a new roll of filament and printer parts, so I can't spend anything.
The first part to print was the filament roller. This is the support for the spool of plastic wire as it sits in the dry box. I wanted to get it started printing before starting any boxes because:
- It printed in two eight hour prints, so best to get it started.
- While it printed, I could work on the other parts. I like that I can be getting two things done at once by printing things while I work on other things.
Printer enclosure
After that started printing, I got to work on the printer enclosure. An enclosure for a 3D printer serves to control the atmosphere surrounding your print. Some materials are very prone to warping, especially if they're exposed to extreme temperature fluctuations and air moving across them before the print is finished. Specifically nylon. I insulated the enclosure box because we had some extra insulation and it'll add a nominal amount of heat insulation to the box. The front will be clear acrylic when it's done, but that'll be a minute, as a man scout friend is making it for me.
I woke up early enough yesterday to start the second set of roller parts so they'd be done when I got back from work.
After assembling the part, I set up the direct drive mount and got it printing, then went to make the dry box. The dry box is needed because nylon filaments suck in moisture from the atmosphere. Before printing, filament needs to be ran through a dehydrator, then kept in a dry box with silica gel during printing and storage. I measured the height and width of the new roller, added the height of a spool of filament, and added a couple of inches to accommodate a larger spool if I ever need to use one.
Filament dry box
The direct drive mount was a fast print that was done shortly after making the dry box. A direct drive extruder is much more precise than a standard extruder, called a Bowden tube extruder. The Bowden tube extruder mounts the filament drive motor away from the hotend where the filament is melted and deposited into the print surface. There's about a foot long tube that the filament runs inside to get to the hotend. A direct drive extruder mounts directly to the same gantry as the hotend and feeds through about an inch of tube, which makes for more precise feeding of the filament. The mount I used retains all the factory hardware and requires no additional modification.
I'm pleased with how the print came out, that's one of the best ones yet. This piece also has a mount for an automatic bed levelling device that I want to get later on, which is convenient.
All stacked up it looks something like that. Now I need a few more bucks to get an extender cable to run the relocated extruder motor, and then I need filament because I don't think I have enough to print anything. There's projects that need printed... Those bits take money, so they're waiting til later. Things are too tight right now to afford printer parts out of my paycheck, so hive and the Bitcoin surge are funding those projects right now.
How was that for a guilt trip to get you to upvote my post? Vote so Nate can buy some things!
Hope you enjoyed it and can get something for the time you spent reading!
Love from Texas
Nate 💚
Dang the future is getting crazy. Pretty soon we can just print out our deceased ones!
Hmm a printed coffin, or a printed and reanimated Aunt Linda?
I dunno Linda gave some pretty good Christmas presents. lol
Done. I'll print two of her.
A 3D printer is pretty cool. What happens to the print material of stupid things that get printed? Is it recyclable? Can you melt it down to make other things?
It's totally recyclable! Actually, the stuff I've been using is even biodegradable and plant based from some kind of sugar cane or something. But I've got a buddy now that also has a small scale recycling setup that can take the old stuff, chop it, melt it, and turn it into new filament, so I've been saving all my little pieces.
Great project, I tried to build myself a dry box for filament but it didn't worked out...
Posted using Dapplr
Thanks for stopping by and following!
What went wrong with your build?
I got my printer in a Box and I put another box from ikea on top where the filament should sit, but the distance was to big and the friction to high...
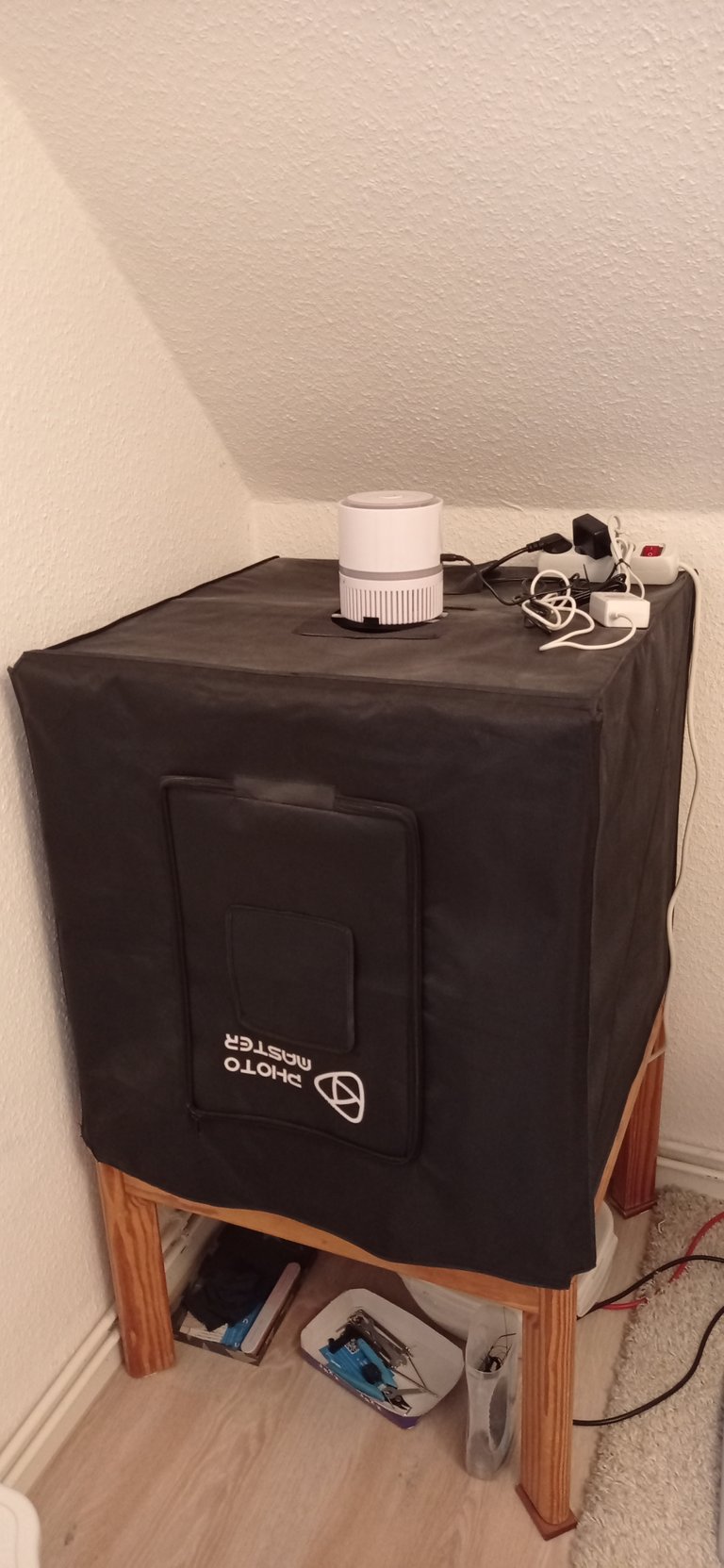
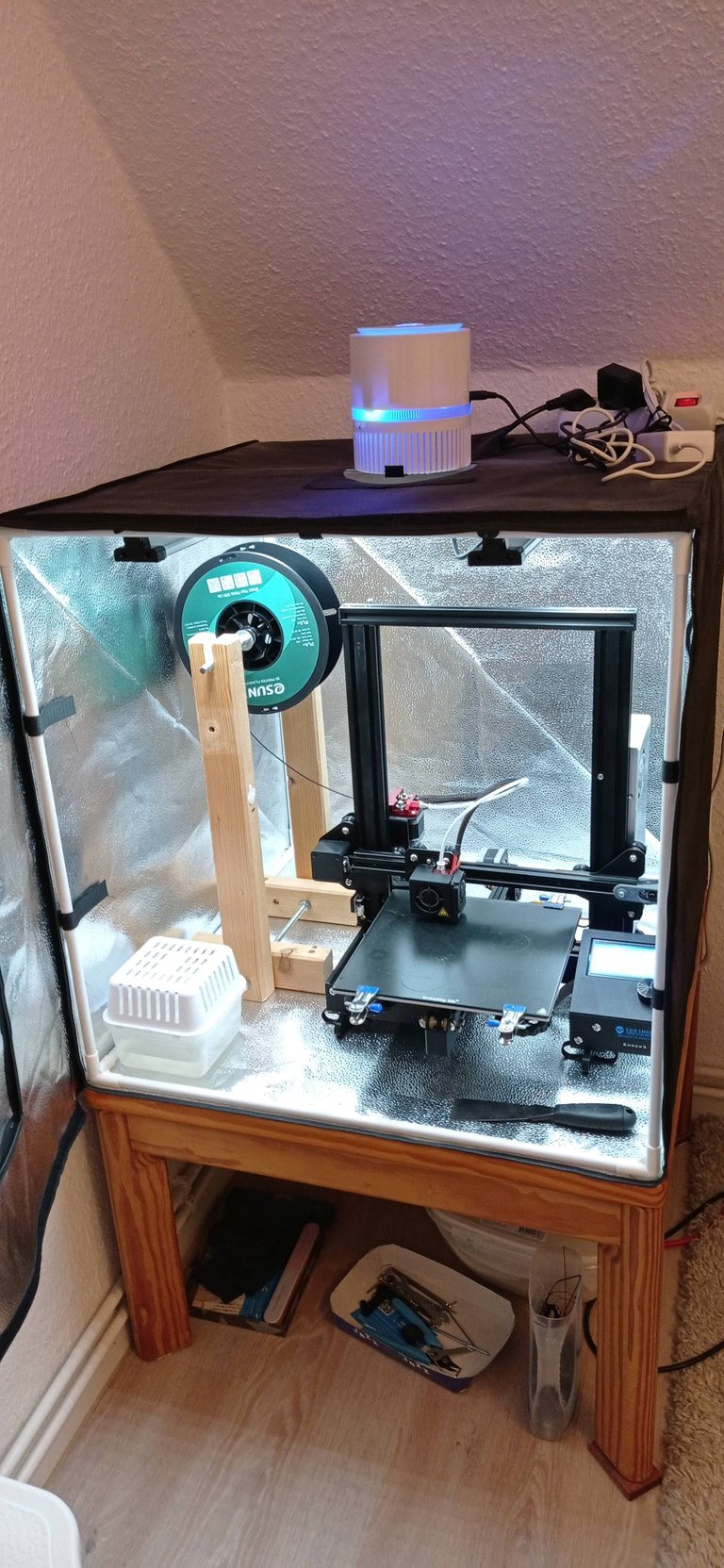
I would like to see your results with the nylon filament, I tried to print it too but the results were disappointing
Posted using Dapplr
Oh, i really like your enclosure there! I like that the filament is in with it. Mine, the filament sits on top and feeds through a hole I drilled in the top. I'm going to do that differently though, and put my old Bowden tube through the top to reduce friction. I don't think my extruder appreciated pulling the filament through the wooden hole with all the friction...
Thank you, it's a photo box that I bought on ebay for a low price + it came with integrated lights
But did you had any problems getting the filament stick to the printbed?
Posted using Dapplr
No, it stuck to the standard print bed just fine. I treat my bed with glue stick now and then cause I heard it helps with adhesion as well as removing the printed parts. I'll do the same with the glass bed too when I get it set up because it's worked so well.