Hello once again and welcome to my blog. It’s another day and another opportunity to explore the beautiful world of engineering. I am glad to announce to you that I got a name from one of my readers on my last post, I think the name should stick - therefore, I would be using the title “steemit mechanic” (how cool is that?) however, today I would not be talking about the automobile or any engine related to it but I would be talking about a process by which the distinct parts of an engine or machinery can be produced – stay tuned!
We live in a world where engines and machinery are part of our everyday lives. From the simple generator, motor cycle or the automobile (yes, I would still mention the automobile) to the big industrial plants the aircraft and ships. Quite inevitably, we cannot get enough of these machines. For a while now, I have been writing about the automobile, processes and parts that are involved in the operation of the automobile. Parts that are sometimes found in other engines and machinery. I have now come up with a question - how can these parts be produced?
One thing worthy of note is that the automobile and other machinery are made extensively of metallic parts. The gears, the screws, bolts, nuts, shafts and a host of others. Here is a question; have you ever taken some time to ask; “how did these parts come to be?” did they just fall from the sky or they are found in the soil of the sea? Well, I would gladly answer you NO!
It is no news that these machine parts are made of metal (obviously). The metals; Iron, aluminium, copper, zinc and the likes in their raw form, are extracted from the earth and processed into sheets, rods, plates and several other shapes.
How then did we get the precise parts of the engine? Well, here is another answer for you.
Some of these parts (and a whole lot of others) can be gotten from the raw materials by casting them (i.e. melting the metal and pouring the liquid metal into a mould where the metal is allowed to solidify and take the shape of the mould). Casting can be used to produce parts that have complex shape or are relatively large. Parts of the automobile engine that are usually cast are the engine block However, some of these parts need to be produced in a more precise and cannot be gotten by casting. Another process by which these machine parts can be produced is known as MACHINING and that’s what I would be discussing today.
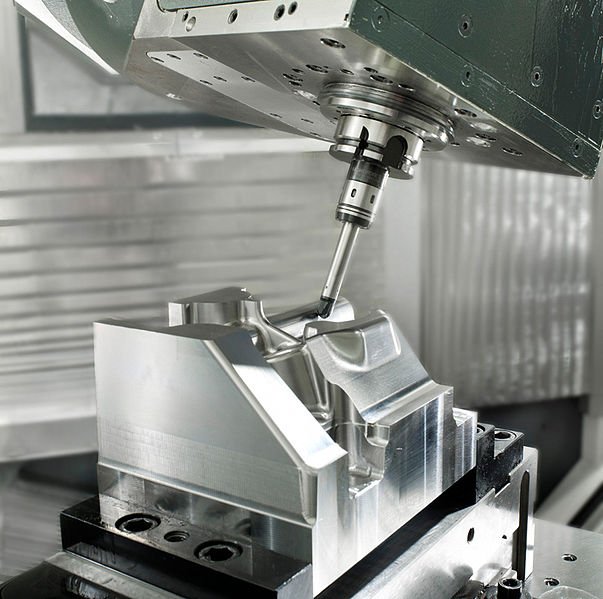
image source: wikimedia commons under Creative Commons Attribution-Share Alike 3.0 Germany license
MACHINING
When I was in my third year in the university, I was opportune to be an intern at a machine shop (that’s what a place where machining operations are done is called). I was able to gain first-hand information about how these simple machining processes are done. Working with the various machines and creating different geometries and shapes.
Alright let’s define machining
Machining is the process by which a desired shape or geometry is derived by removal of parts of a raw material in a controlled manner using a special type of machine.
just like sharpening a pencil requires the removal of the outer wooden part. Or sculpturing requires carving the wood to create the shape required, machining is a more precise way of creating shapes (of machine parts) with the aid of a machine. (that wasn’t so hard to say, was it?)
Machining is a very versatile process of manufacturing and can be used to produce different geometries and features of machine parts. It is preferred to casting as the produced parts from machining are precise and accurate. In manufacturing terms, machining operations are often categorized under subtractive manufacturing as they involve the removal of materials in order to achieve the desired geometry.
Machining operations achieved by the removal by the relative motion of a tool against a piece of material (known as the work piece). However, machining does not apply to metal products only, materials such as wood, ceramics or plastics can also be machined to derive the required geometry.
The machines used to carry out machining operations are known as machine tools. These tools have been around for a while and have found application in the general production of machine parts such as gears, shafts, screws, nuts, bolts and a whole lot of other machine components. The machine tools are totally important and are still relevant till today.
I used to call machine tools “super machines” because they are machines that produce machine
How about a look at the “super” machines that are used to produce these parts.
THE LATHE
Say hello to the big boss of machine part production; the lathe. The lathe is a machine tool in which the workpiece (material to be machined) is rotated about an axis while a tool (the material used to cut the workpiece) is moved against the workpiece by the operator.
The lathe comes in a variety of types and sizes but for the sake of this post, I would be concentrating on the metal working lathe (they are all similar). The lathe is usually driven by an electric motor connected to a large train of gears which can be adjusted for speed selection. The lathe is generally used to work on cylindrical materials.
The distinct parts of the lathe include the head stock which contains the control panel and the spindle where the work to be machined is mounted, the tool post which is where the cutting tool is mounted, the tailstock which is used to hold tools such as drills or center rests for holding the work piece on the other end.
The metal working lathe is basically used for small and medium production and can be used to perform a variety of operations including;
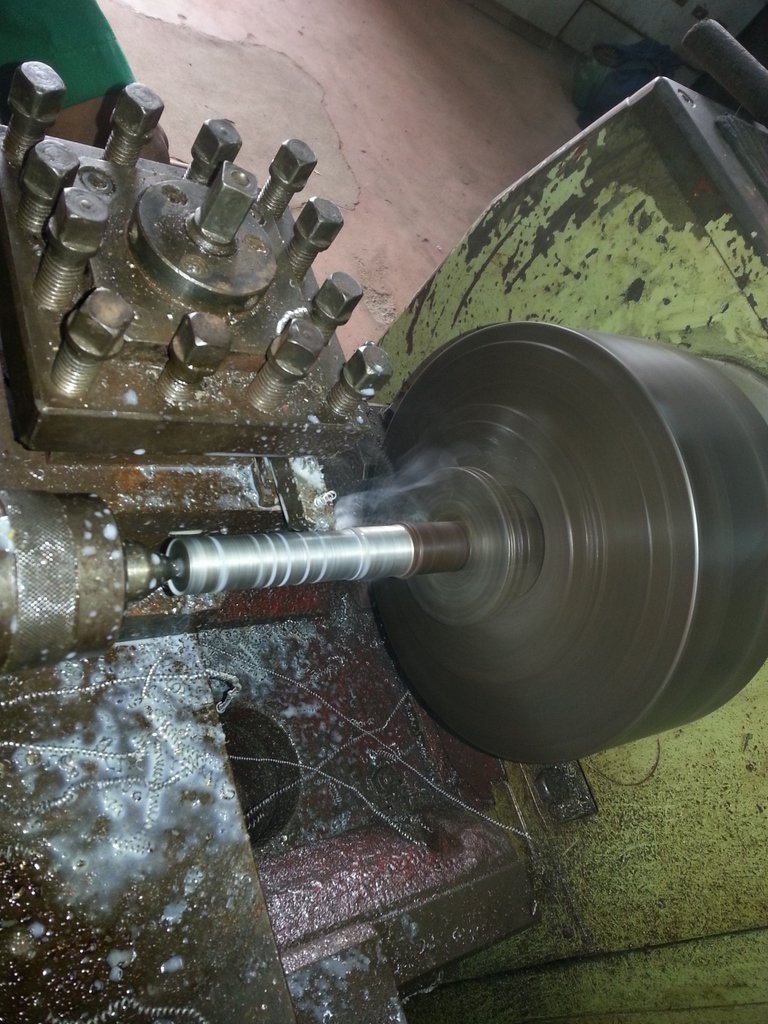
TURNING OPERATION (image taken by me)
- TURNING
This is quite the basic job of the lathe. It involves the use of a single point tool to remove material from the surface of the workpiece. The workpiece rotates at a set speed on the lathe while the tool is fed (moved) towards it. The direction of movement of the tool is parallel to the axis of rotation of the workpiece.
Turning operation produces cylindrical shaped materials and is basically the reduction of the diameter of a material. Machine parts such as shafts, rods and the likes are produced by turning the input material on a lathe.
Other forms of turning operation include; taper turning which is simply turning at an angle i.e. the final product is of a conical shape. Step-turning which is the reduction of the diameter of different parts of the workpiece. Form turning which involves the use of a special type of tool to make the required shape on the material.
In the instance where the operation is done at one point of the material and is allowed to cut through, the operation is known as parting off. Other types of turning operation include the contour turning, form turning and chamfering (turning at an angle).
- THREADING
The lathe machine is also used to make threaded materials such as bolts. It is very efficient and more precise than the manual threading tools. The thread patterns that a lathe can create are numerous and can be of numerous pitch and dimensions. Machine parts that are produced by threading include the bolts and threaded shafts.
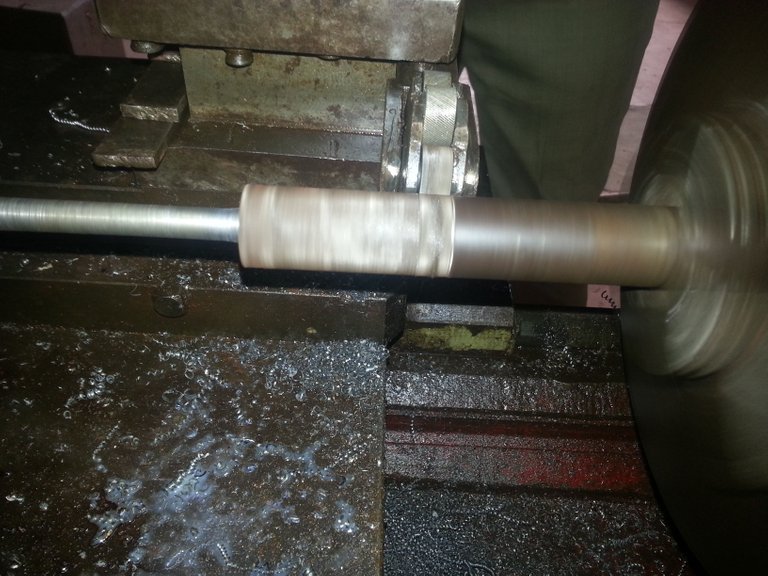
KNURLING OPERATION (image taken by me)
- KNURLING
Although knurling is not a machining operation (it does not involve the removal of material), it is one of the operations that a lathe can be used for efficiently. Knurling is the process of creating a pattern on a material, usually a hatched pattern on the surface of the workpiece. Knurling is usually done on materials that are intended to be used as handles.
The knurling operation makes use of a special tool called the knurling tool.
Other operations that the lathe can be used for include; drilling (yes, drilling). In this case, the material to be drilled is set on the lathe and the drill bit to be used is mounted on the tool post. The drill bit is then fed into the material. However, this does not substitute for the use of drilling machines.
All in all, the lathe is a very important tool in the machining of machine parts (I guess I have mentioned the word “machine” the 1000th time here). It is efficient and standard. The lathe can be operated manually or sometimes can be put into automatic working after some initial input by the operator.
The conventional lathe needs to be manned at all times while in operation to ensure accuracy and precision.
THE MILLING MACHINE
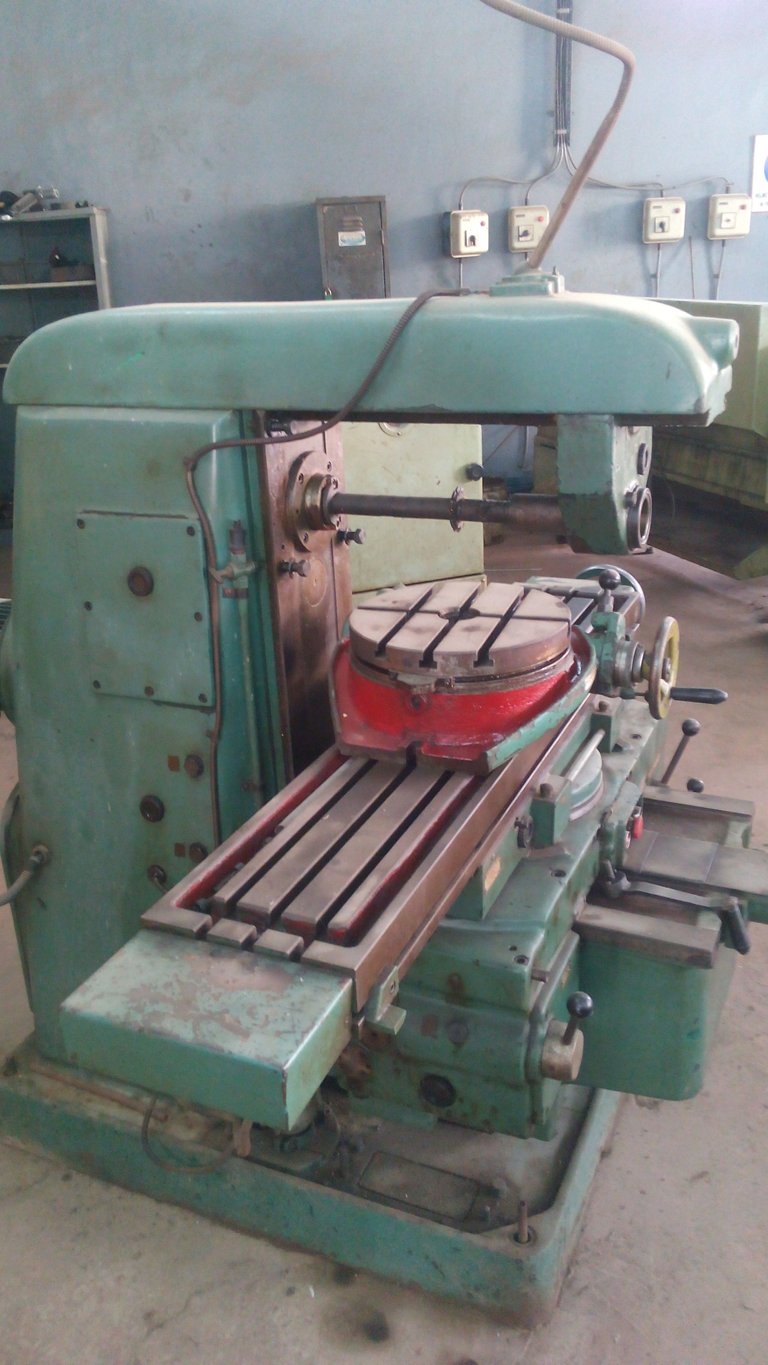
THE MILLING MACHINE (image taken by me)
The second “big” machine used for machining operations is known as the milling machine. This machine is also driven by electric motor and a gear train that can be adjusted for speed but in this case, it uses a rotating cutting tool to remove material form the workpiece which is fed (moved) against the cutting edges of the tool.
The type of cutting tool that the milling machine uses is known as milling cutters and they are multiple point cutting tools (I.e. they have more than one teeth for cutting). The process involves removal of material in small separate cuts.
The milling machine is used for a wide range of operations and can be used to machine a lot of machine parts.
The milling machine is one of the most commonly used for machining of custom parts to precise tolerances.
The distinct parts of the milling machine include the head which contains the spindle where the tool is mounted , the worktable where the workpiece is mounted and fed to the cutting tool (the work table can be moved in multiple directions along the X,Y and sometimes the Z axis), the knee and base.
The milling machine comes in two types of orientations; the vertical and the horizontal. The major difference between the vertical and horizontal milling machines is that the orientation of the spindle. The vertical one has a vertical spindle while the horizontal has a horizontal spindle.
The operation of a milling machine can be classified into two categories;
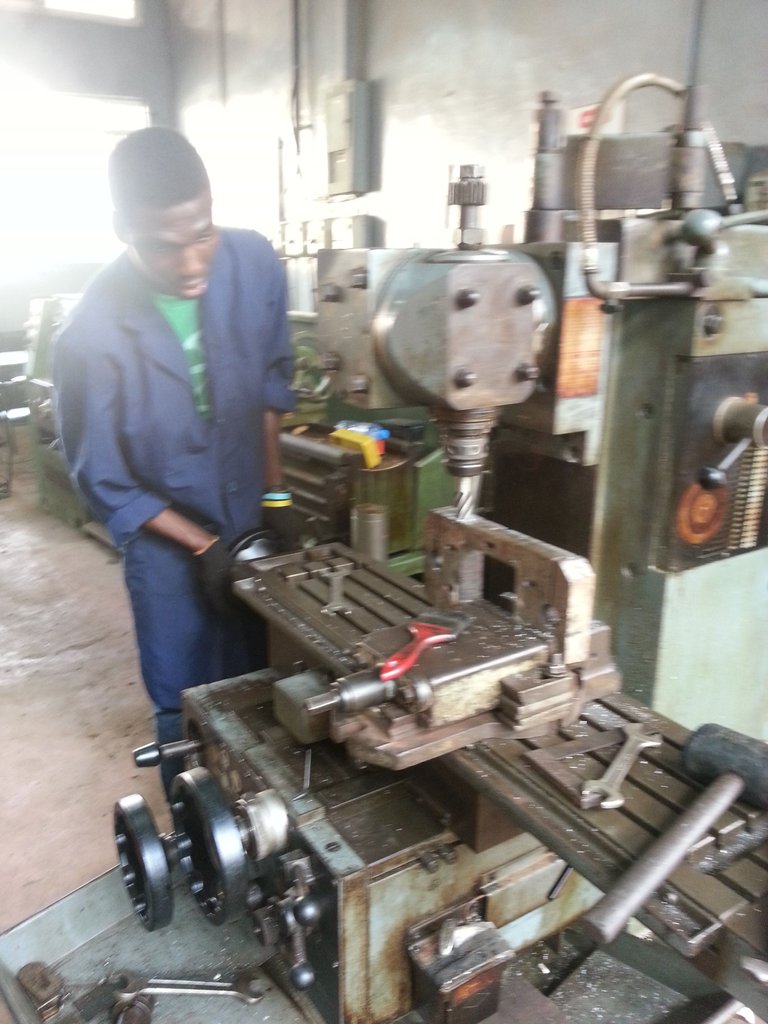
YES, THAT'S ME USING THE MILLING MACHINE (image taken by me)
FACE MILLING
This type of milling is one which the cutting is done at the end corner of the cutting tool. Here, the axis of rotation of the cutting tool is perpendicular to the surface of the workpiece. When there is the need for cutting a flat end surface or cavity, the face milling is done.PERIPHERAL MILLING
This the type of milling where the tool axis is parallel to the surface of the workpiece. The cutting action therefore occurs at the circumference of the cutter.
Peripheral milling is the type of milling that is applied when cutting gear teeth, threads and deep slots
The milling machine can also be made to perform gang milling where more than one tool is mounted on the machine to cut the material at the same time.
Machine parts that can be produced on the milling machine include; gears, nuts, flat surfaces
A NUT BEING MACHINED (image taken by me)
THE DRILLING MACHINE
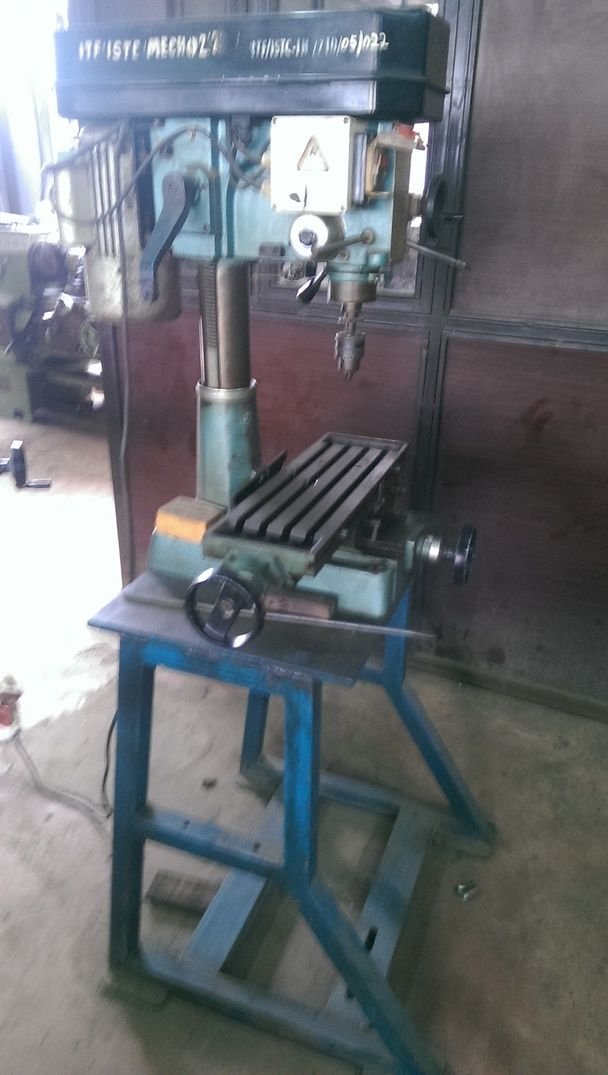
THE DRILLING MACHINE (image taken by me)
Although the lathe and milling machine can perform some sort of drilling, the drilling machine is also a machine tool that finds relevance in machine part fabricatrion. I am quite sure a lot of us are familiar with this machine tool as it has smaller versions that are handy and are used in our daily minor operations.
The drill machine is also an important tool which is used to make holes of different sizes on a workpiece. The machine uses electric motor and belt drive to rotate a multipoint cutting tool known as the drill bit. The drill bits come in various diameters depending on the size of the hole to be created.
In drilling, the material to be drilled is mounted on the work table and the drill bit of the required diameter is attached to the spindle of the machine. The speed is also selected. the drill bit is then lowered into the workpiece gradually. A coolant fluid is applied to cool the tip of the bit to prevent it from breaking as a result of the excess heat.
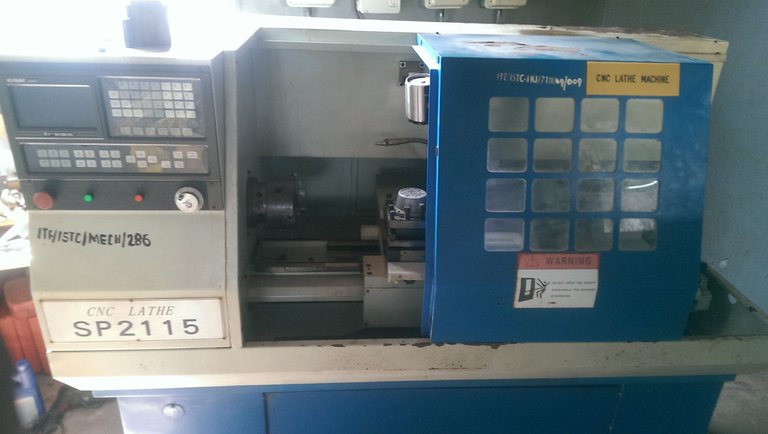
A CNC LATHE (image taken by me)
THE CNC MACHINES
Maybe you have been wondering, how these machines can be used to produce a large number of engine parts efficiently and conveniently if they are manually operated. Well, search no further, there are the automated machine tools known as the CNC machines.
CNC stands for Computer Numerical Controlled and is a computer program that is integrated into machine tools for the automation of the machining processes. The CNC machine tools are used in industries where the machine tools are required to produce parts in a high number, efficiently and with high precision thereby eliminating the chances of human errors in machining in the case of using conventional machine tools.
The CNC types of machine are available for lathe and milling machines. The part to be machined is usually designed using Computer Aided Software including the dimensions and all required properties. This is then translated into computer codes that would be interpreted by the machine to perform the required task. The CNC machines make use of codes known as the G and M codes.
You could also be considering the fact that a part might require different processes that need different types of cutting tool. Well, the CNC machines are equipped with tool holders that can hold different types of tools at a time. The order of operation of these cutting tools is usually incorporated into the command codes put into the machine.
The existence of the CNC machines however have not stopped the use of the conventional manual machine tools as these tools still find application in various sectors of the engineering world where automation is not totally required.
CONCLUSION
There we have it, all the parts of a machine did not drop from the sky (obviously not). They were fabricated using the almighty “machine tools”. Yes these tools are the one that birth all other parts of machines and engines.
Therefore, next time you see a piece of machinery with exposed parts or you are opportune to handle a simple part such as a shaft, gear or something like that, take time to appreciate the lathe, milling or the drill. They made this possible!
There are some other machines that in one way or the other, are also involved in the production of parts, some of these machines are ; the plasma cutter, the electronic discharge machines, the water jet cutter e.t.c
I would leave you with this video of how the piston (one of my favorite parts of an internal combustion engine) is fabricated.
REFERENCES
1. MACHINING
2. METAL WORKING
3. LATHE
4. MILLING
5. NUMERICAL CONTROL
6. Fundamentals of modern machining (textbook) by Mikell P. Groover
Let me comment in GM codes.
Y 50 X 00
Y 00 X 30
Y 50 X 00
Y 00 X 00 Z -1
☺ ☺
haha you remember the codes!
Yeah I do, nice posts about machining bro.
Thanks
I even engraved my name on a metal using these codes. The idea is like plotting a graph.
Exactly, if u can draw the graph, you can write the code.
I worked on the lathe machine sometime last year and it was a wonderful experience that was where i saw gears being produced for the first time.
I would be resuming back to know more about these operations and parts of the machines.
Wow. I agree with the fact that it is always a wonderful experience machining these components.
It is nice to know that you want to continue the learning. All the best sir
Thank you.
Machining is a very important aspect of production. In fact a substantial portion of the practical field of production engineering is dominated by machining.
Machining is one tool that has allowed us replace component that are scarces or not available in the market. Most production company, like a power generating station for instance have machine shop for this reason. In an event of any breakdown, they can easily fabricate spares.
Well done sir.
Rightly said sir. Without machining, there won't be machines.
Yes, machining is very crucial in manufacturing. Wonderful post sir.
By the way, the name steemit-mechanic will fit perfectly. This is very "mechanical"
Thank you for stopping by sir!
Yes, the name has stuck.
These machines play a vital role in enabling manufacturing companies in advanced industries to deliver components and products to the highest possible specifications.
They also provide the basis for precision manufacturing... BTW... The steemit mechanic is the coolest!!!😀
I'm to say I gave you that name!
I thought you said you wouldn't be talking abt Automible, your examples are almost all automobile..You're always the steemit-mechanic
Machining is a top top engineering process that can never be ignored. We need to make our parts and it is one of the great way to achieve this
I had experience of working at such workshop too and I'm quite familiar with the lathe and Milling machine as well..Well done
Nice Input
yeah you gave me that name. lol, i just cannot get enough of the automobile... don't mind me.
thank you for dropping by
You're welcomed
Alot about machine tools well said by you. Thanks to mother LATHE MACHINE that give birth to the others machines. 👍 @rharphelle.
thank you for visiting my blog!
Just last year, I was opportune to spend my holiday working at a machinist shop. That was when I learnt how to use the lathe machine. The lathe machine can perform quite a range functions. Can even do the work of a drilling machine. Nice article @rharphelle
wow i am sure it would be an awesome experience
Good one on Machining @rharphelle
Enjoyed reading through..
thanks for dropping by
This is "How it's made", Steemit edition. You know, the Discovery Channel show that was very popular?
How is the technical education going on in your country?
Are the students aged 12-18 involved in such technical classes? How does one get to practice mechanics before actually choosing to specialize on it?
Here, it's mandatory to have mechanical classes if you follow a technical complementary school (and I think it's mandatory even if you are not, but for the girls there are sewing classes as an option). Again, I don't know exactly how it is now, it was like that 15 years ago although I think it's more of less the same.
This gets kids to get to know if they like it.
I do not really know the show on discovery channel.
Technical education here is quite fair, i know quite a number of skill acquisition schools where technical courses are taught. I actually did a 3 month internship in one of them. Although some students are exposed to more of theory than the practicals.
Thank you for dropping by, i am honored!